Gary Horgan (CMSE Consultancy Manager at the Chris Mee Group) and his team are outlining the path for companies to ensure they are compliant with Part 8 “Explosive Atmospheres at Places of Work” of the Safety, Health & Welfare at Work (General Application) Regulations 2007 in a series of focussed blogs.
This is blog number 9 in the series, written by Denis Mulcahy.
- Blog 1, Explosion Accidents 2020
- Blog 2, Preparing for an Explosion Protection Document
- Blog 3, Summary of Legal Requirements
- Blog 4, What Are Explosions?
- Blog 5, Characteristics of Flammable Liquids, Gases and Vapours
- Blog 6, Characteristics of Combustible Dusts and Powders
- Blog 7, Hazardous Area Classification – Dusts
- Blog 8, Hazardous Area Classification – Liquids, Gases and Vapours
- Blog 9, Static Electricity as an Ignition Source
When we consider potential ignition sources we may think of open flames and sparks from grinding and welding operations, which are a significant contributor to the ignition of flammable or explosive atmospheres, accounting for approximately 22% of all ignitions. However, static electricity also accounts for approximately 22% of all ignitions.
- Creation of electrostatic charges
An electrostatic charge occurs whenever two surfaces are separated, where at least one of them is highly electrically insulating. When two surfaces come into contact, a redistribution of charge carriers takes place. The phenomenon applies to both solids and liquids depending on electrical conductivities.
People can become charged by walking across a room where either the carpet or their shoes are nonconductive. High charges can also be created on conveyor belts and during the unwinding of plastic films. When a powder is unloaded, conveyed through a pipe, is sifted, or fed through a funnel, the powder and equipment will probably become charged. Similarly, with liquids, flow through pipes or hoses, stirring, spraying or liquid atomization, will probably cause both the liquid and equipment be become charged.
The charge level may be increased for liquid flow through filters or where multiphase mixtures are handled. For example, liquids that contain suspended solid particles or droplets of an immiscible liquid, the charge level will probably increase by several orders of magnitude.
- Types of Electrostatic Discharges
2.1. Spark discharges
A spark discharge can occur when the charge potential rises to the point where the dielectric strength (resistance) of the air is reached across a suitable sparking gap to an earthed object.
The energy W of such a spark discharge can be calculated with the formula W = ½ CU2 where C represents the capacitance of the insulated, conductive object and U its potential.
The ignition danger is assessed by comparing the discharge energy with the minimum ignition energy of the potentially explosive atmosphere present. This will show that flammable gases, vapours, and dusts can be ignited by spark discharges.
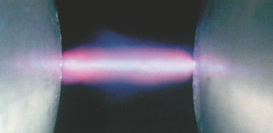
Where charges are restricted to nonconductive surfaces, they cannot be dissipated in the form of a single spark discharge. Under these circumstances, there are three other types of discharge that may take place.
2.2. Brush and corona discharges
Where the surface of an insulator has charges of one polarity which are raised to the level equal to or greater than the dielectric strength of air (approx. 3× 106 V/m). A static discharge can occur when surface of an earthed electrode (e.g. person’s finger) nears the surface.
Corona discharges generally occur if the electrode’s diameter is approx. 1 to 5mm. For larger electrodes brush discharges are more probable. For hazard assessment, the worst-case i.e. a brush discharge is usually considered.
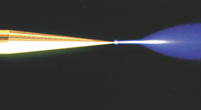
Brush discharges can also be expected when an earthed, conductive electrode enters a high-strength electric field. The electric field may be created by a highly charged insulating liquid or suspension, a mist, a pile of insulating bulk solids, or a dust cloud.
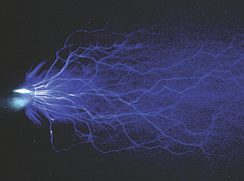
The characteristic properties and incendivity of brush discharges have been studied by many authors. The figures stated in the literature for the equivalent energy of brush discharges, which were determined with explosive gas/air mixtures, are on the order of a few millijoules.
The incendivity of bush discharges depends on the electrode’s radius of curvature, the polarity of the electric field, and – if the electric field emanates from a charged plastics surface – the surface charge density and size of the charged surface area.
Energy released from brush discharges is assumed to have the potential to ignite explosive gas/air mixtures, vapour/air mixtures and hybrid mixtures but are very unlikely to ignite pure dust clouds.
2.3. Propagating brush discharges
Where charges of opposite polarity occur on the opposing surfaces of an insulating sheet, propagating brush discharges can occur. They are caused by an electrical short circuit between the two oppositely charged surfaces of the sheet.
These can typically arise when:
- When two electrically connected electrodes approach the respective surfaces or
or
- Mechanical perforation of the sheet
or
- Electric perforation of the sheet i.e where the charge density is sufficient to overcome the resistance posed by the weakest point in insulating sheet.
The resulting brush discharge forms a bright central discharge and many discharge channels propagate outward along the surface point like the spokes of a wheel on both sides
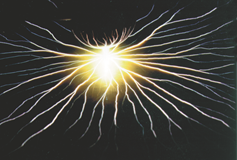
The energy released by propagating brush discharges is normally sufficient to ignite potentially explosive gas/air, solvent-vapour/air, and dust/air mixtures.
Persons may suffer serious shock if, for example, they initiate a propagating brush discharge by inadvertently touching a highly charged surface. Efforts must be taken to exclude this kind of discharge wherever potentially explosive gas, vapour or dust atmospheres can form.
2.4. Cone discharges
These discharges may occur when charged and highly insulating solids i.e. with volume resistivities greater than 1010 ohms·m are filled into silos and containers. Although silos may be conductive, and earthed, for highly resistive solids subjected to high filling rates, the charge dissipation time may not be sufficient. The charges on the surface of the solids may accumulate to a point where the dielectric strength (resistance) of the air within the silo is reached and the solids are piled and form a suitable gap to allow a discharge from the surface of the solids to the earthed side of the silo.
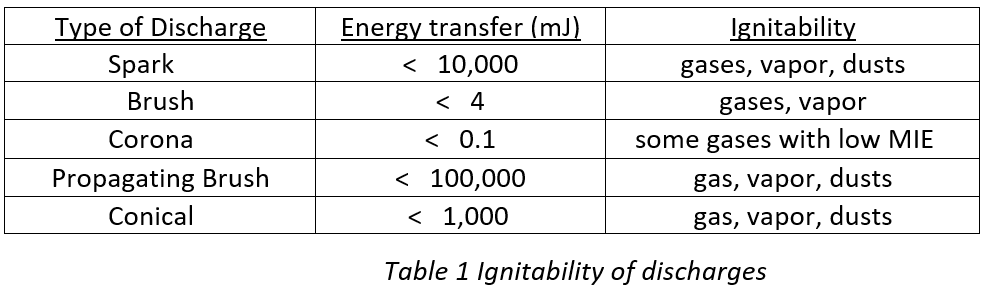
- Controlling Static Electricity
Earthing & Bonding
The most important protective measure is to connect and earth all conductive parts that might become dangerously charged.
Some examples of earthing and bonding arrangements
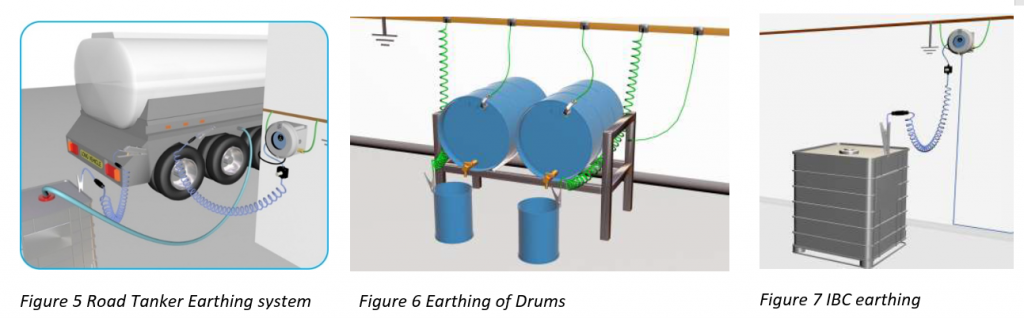
However, if nonconductive parts and materials are present, earthing and bonding may not be enough. In such cases, dangerous charging of nonconductive parts and substances (including solids, liquids and dusts) must be excluded by other means such as
- Control of filling velocity
- Avoiding splashing – fill from the bottom.
- If mixing liquids consider density and miscibility.
- Consider charge relaxation time for non-conductive liquids or resistive solids
- Use of static dissipative additives to assist with charge relaxation.
- Use Static Dissipative Floors however, if the floor is not conductive, a grounded mat may be used.
- Use anti- static PPE
- Earth Continuity Testing
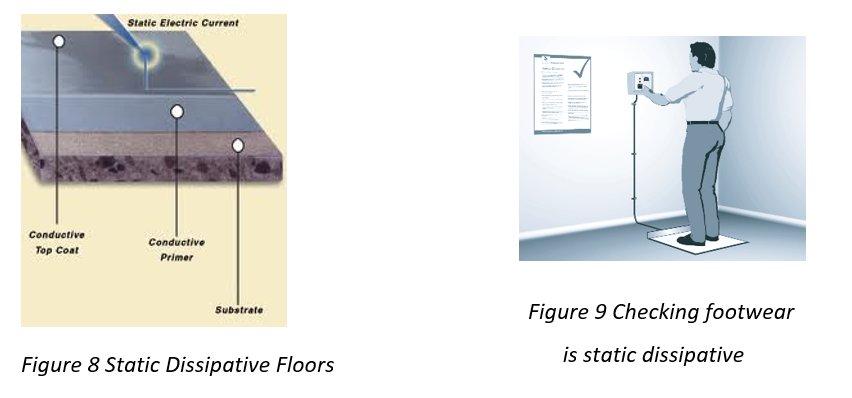
Sign up here to receive the next article in this series directly to your inbox before it goes live to the public
CMSE Consultancy provide a professional Health, Process, Explosion & Fire Safety Services.
If you require further information or assistance please contact us via email at info@cmse.ie, by phone at 021 497 8100 or start an instant chat with us via the chat box in the bottom right-hand corner of your screen.