Gary Horgan (CMSE Consultancy Manager at the Chris Mee Group) and his team are outlining the path for companies to ensure they are compliant with Part 8 “Explosive Atmospheres at Places of Work” of the Safety, Health & Welfare at Work (General Application) Regulations 2007 in a series of focussed blogs.
This is blog number 13 in the series, written by Jake Bumpus which deals with Organisational Control Measures to prevent and mitigate explosions.
- Blog 1, Explosion Accidents 2020
- Blog 2, Preparing for an Explosion Protection Document
- Blog 3, Summary of Legal Requirements
- Blog 4, What Are Explosions?
- Blog 5, Characteristics of Flammable Liquids, Gases and Vapours
- Blog 6, Characteristics of Combustible Dusts and Powders
- Blog 7, Hazardous Area Classification – Dusts
- Blog 8, Hazardous Area Classification – Liquids, Gases and Vapours
- Blog 9, Static Electricity as an Ignition Source
- Blog 10, Non Electrical Ignition Sources
- Blog 11, Equipment Selection for potentially Explosive Environments
- Blog 12, Engineering Control Measures
- Blog 13, Organisational Control Measures
In the previous blog, we discussed the physical measures businesses can implement to prevent and/or mitigate explosions – generally referred to as engineered or technical control measures. However, as a reminder, Regulation 171 of the General Application Regulations 2007 states that “an employer shall… take technical and organisational measures that are appropriate to the nature of the operation”.
There is therefore a duty on employers to not only consider the physical controls, but also what organisational controls should be implemented to prevent and/or mitigate explosions in their workplace. In this blog, we will discuss some common organisational controls which should be considered by employers who operate workplaces where there is the potential for an explosive atmosphere to form.
Standard Operating Procedures/Written Instructions
Work in hazardous areas should be carried out in accordance with written instructions, which are commonly referred to as Standard Operating Procedures (SOPs) in many workplaces. Written instructions cannot by themselves prevent accidents, but they are an important part of providing a safe system of work, particularly when working in hazardous areas.
It is important that all workers are made aware of the relevant written instructions as part of their training to undertake a task safely, and that any important safety considerations are highlighted.
As well as recording the normal operation of a task, written instructions should also include how to respond to any reasonably foreseeable abnormal events, such as equipment failures, spillages, leaks etc.
Permit-to-Work System – Hot Work Permits
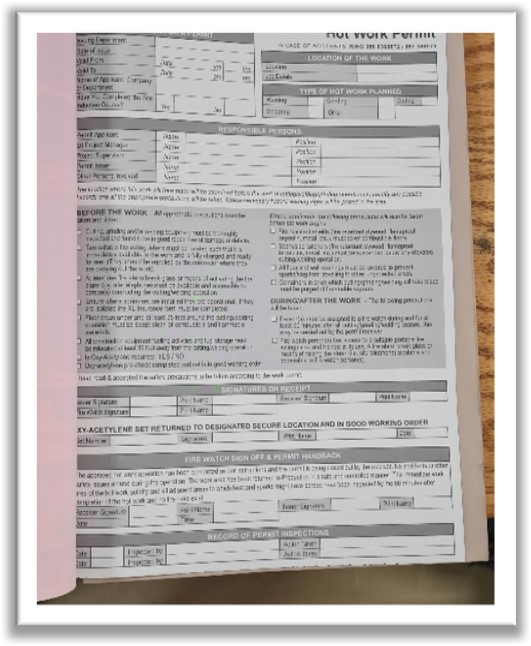
A permit-to-work system is a specialised type of safe system of work for ensuring that potentially very dangerous work is done safely. The fundamental principle for this type of system is that certain defined operations are prohibited without additional controls and the specific permission of a responsible manager.
Hot work includes cutting, welding, brazing, soldering, drilling, grinding, and any process involving the application of a naked flame. Hot work in a potentially explosive atmosphere is very hazardous because it can be a source of ignition. Hot work should therefore be done only under the terms of the hot work permit, the only exception being where hot work is done in a designated area suitable for that purpose (e.g. welding in a dedicated welding booth).
Typical types of protective measures that might be introduced by a hot work permit include:
- the removal/isolation of flammable materials from the area,
- testing/monitoring for flammable gases,
- additional fire fighting equipment (e.g. fire extinguishers/fire blankets)
- fire watch
Training
According to Regulation 173 of the General Application Regulations 2007, employers are required to “provide persons at work in workplaces where explosive atmospheres may occur with sufficient and appropriate training with regard to explosion protection”. The duration and complexity of the training required should be determined by the employer, and will be different depending on the duties and responsibilities of the workers concerned.
For example, general explosion safety awareness training may be sufficient for general operatives working in hazardous areas in accordance with well-understood written instructions. We would recommend that to be most effective even general awareness training should include elements that have been made bespoke to the particular workplace (e.g. include photographs/drawings of the hazardous areas that have been identified on site).
For workers who require a more detailed understanding of explosion safety topics, such as managers and supervisors, CMSE Training run a 3-day Explosion Safety Management course which is externally accredited by IOSH.
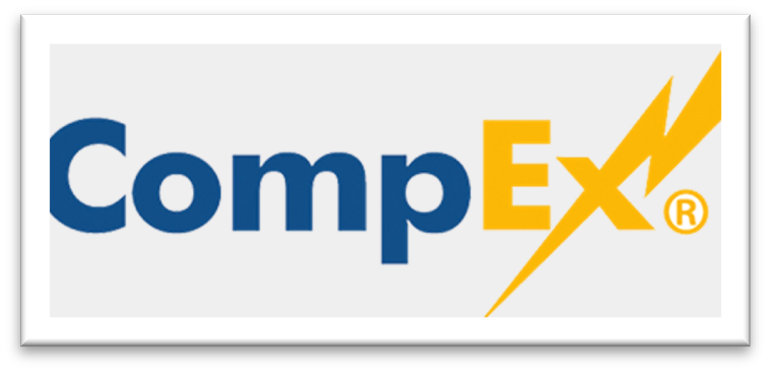
For more specialised workers, e.g. engineers/technicians who are required to install, commission, and inspect Ex-rated equipment, then more in-depth training will be required to ensure that they are suitably competent for the role. Although not specified in legislation, we would recommend that these types of workers undertake CompEx training, as it is considered industry best practice. CompEx is an internationally recognised training qualification for Electrical, Instrumentation & Mechanical Engineers and Technicians who need to develop and demonstrate their competency in the selection, installation, inspection, and maintenance of Ex-rated equipment in potentially explosive atmospheres.
Planned Preventative Maintenance (PPM) Programmes
It is very important that all Ex-rated equipment is included in a programme of planned preventative maintenance (PPM). Inspection and maintenance should be undertaken by suitably trained and competent personnel, and should be carried out in line with the frequencies outlined in EN 60079-17:2014 “Explosive atmospheres. Electrical installations inspection and maintenance”.
Regular inspection and maintenance of Ex-rated equipment is critical, as otherwise there is a potential that equipment that was previously safe to use in a hazardous area could become damaged/defective and subsequently act as an ignition source in an explosive atmosphere.
We will discuss inspection and maintenance of Ex-rated equipment in more detail in the next edition of this process safety blog series.
Sign up here to receive the next article in this series directly to your inbox before it goes live to the public
CMSE Consultancy provide professional Occupational, Process, Explosion & Fire Safety Services.
If you require further information or assistance please contact us via email at info@cmse.ie, by phone at 021 497 8100 or start an instant chat with us via the chat box in the bottom right-hand corner of your screen.