Introduction
Combustible dust hazards pose significant risks across various industries, from manufacturing plants to food processing facilities. When fine particles are dispersed in the air at optimal concentrations, they can lead to massive explosions and fires. In this blog post, we’ll delve into strategies for eliminating and mitigating dust hazards. We’ll cover essential aspects such as controlling ignition sources, housekeeping best practices and explosion protection measures.
Sources of Ignition for a Dust Explosion
Source of ignition for dust explosions are quite numerous however the most common ignition sources are the following:
- Fires
- Hot Surfaces
- Self-Ignition of dusts
- Friction
- Electrostatic Ignition
Particle Size
An explosion hazard arises when dusts are manufactured, stored, or processed and these materials are airborne. Dust explosions happen when a dispersed flammable element is present in high enough concentration. The likelihood of an explosion rises sharply when the product being processed is thought to be flammable and contains a sizable amount of fine material. Along conveying systems, fine powders with low minimum ignition energies (MIE) will inevitably approach the minimum explosive concentration (MEC) and may be susceptible to combustion from several sources of ignition. Electrostatic discharge is one type of such ignition source.
The fineness of a particle determines the minimum ignition energy (MIE) needed to ignite any given powder, with very small particles typically requiring the lowest values. Special precautions to reduce static electricity are typically not required if the MIE is above 10 millijoules and there are no flammable gases or vapors present. However, operators may still need to take precautions when using conductive plant equipment that can store high levels of static charge in order to reduce the risk of electric shock.
Addressing Combustible Dust Hazards at their Source
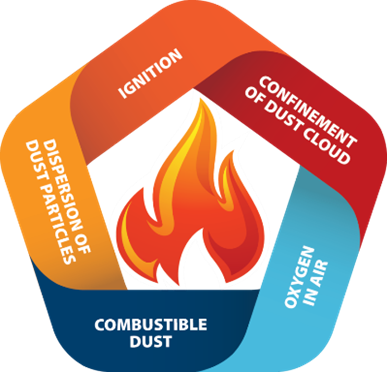
Figure 2 – Dust Explosion Pentagon [4]
- Implement thorough good housekeeping practices to reduce the accumulation of combustible dust on surfaces, particularly floors.
Control of Oxidant
- Aim to eliminate or minimize the presence of oxidants, especially in large – scale operations where controlling oxygen levels may be challenging.
Control of Ignition Sources
- Employ measures to prevent self – heating and spontaneous combustion of materials.
- Identify and mitigate potential ignition sources to minimize the risk of combustion.
Housekeeping Best Practices
- Thoroughly clean dust residue at regular intervals.
- Use cleaning methods that do not generate dust clouds (avoid sweeping with a broom or blowing down).
- Keep control over fugitive dust to avoid secondary explosions outside the processing facility.
Controlling Ignition Sources
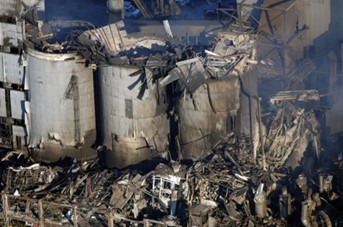
Figure 3 – Dust Explosion Aftermath [7]
Ignition sources can vary widely, including sparks from mechanical friction, electrical equipment malfunctions, static electricity, open flames and even hot surfaces. The challenge in controlling these sources lies in the diversity of potential ignition points and the unique characteristics of different industrial environments. Consequently, a thorough understanding of the specific hazards present in each facility, as well as an approach to risk assessment and management is essential.
In this introduction to controlling ignition sources of dust explosions, we will explore the fundamental principles behind dust explosion risks, the various types of ignition sources that must be managed and the strategies that can be employed to mitigate these risks. By adhering to established safety standards and continuously evaluating and improving safety practices, industries can significantly reduce the risk of dust explosions and protect both their workforce and infrastructure.
Controlling Friction & Impact Sparks
Friction and impact can generate sparks, which are significant ignition sources in dusty environments. These sparks can arise from routine operations involving machinery, tools, or materials that collide or rub against each other.
To mitigate this risk:
- Regularly inspect and maintain mechanical equipment to ensure smooth operation without excessive friction.
- Implement the use of materials and coatings that minimize spark generation during impact or friction.
- Design workflows and workspace layouts to reduce the potential for accidental impacts or friction in dust-prone areas.
Controlling Self-Heating
Self-heating is a phenomenon where certain materials, especially organic materials like grain dust, can undergo oxidation that generates heat. If this heat is not adequately dissipated, it can lead to ignition.
To prevent self-heating:
- Regularly rotate stockpiles and ensure that materials are stored in a manner that allows for adequate air circulation.
- Install temperature monitoring systems in storage areas to detect abnormal temperature rises.
- Train staff to recognize the signs of self-heating and implement appropriate emergency procedures.
Sources of Electrostatic Charge Generation
Electrostatic charges can accumulate and discharge suddenly, causing sparks. This is particularly common in operations involving the movement of powders or fluids.
To address electrostatic hazards:
- Ground all equipment and structures to allow for the safe dissipation of electrical charges.
- Use antistatic or conductive materials for containers, piping, and other equipment that comes into contact with dust.
- Implement humidity control measures, as higher humidity can reduce the buildup of static electricity.
Controlling Electrical Arcs
Faulty electrical equipment and wiring can produce electrical arcs, potent ignition sources.
Ensuring electrical safety involves:
- Adhering to electrical installation standards and regulations specific to hazardous environments (such as ATEX in Europe).
- Conducting regular inspections and maintenance of electrical systems to identify and rectify potential faults.
- Using intrinsically safe or explosion-proof electrical equipment in areas where combustible dust may be present.
Flexible Intermediate Bulk Container (FIBC) Considerations
FIBCs, or bulk bags, are commonly used for storing and transporting powders and granular materials. Certain types of FIBCs can accumulate static electricity, posing a risk in dusty environments.
To prevent incidents:
- Choose FIBCs with appropriate electrostatic properties for the specific application. Type C FIBCs, for example, are conductive and should be grounded during filling and emptying.
- Train staff on the correct handling and use of FIBCs, emphasizing the importance of grounding where necessary.
Ensuring the Use of Suitable/EX Rated Equipment
In environments with explosive atmospheres, using equipment rated for such conditions (EX rated) is essential. This includes everything from lighting and electrical components to hand tools and machinery.
To ensure compliance:
- Conduct a thorough risk assessment to determine the required EX rating for equipment in each area of the facility.
- Procure equipment that meets these specifications and ensure that all equipment is properly labelled and documented.
- Provide training for staff on the importance of using only EX rated equipment in designated areas and the risks associated with using non-compliant equipment.
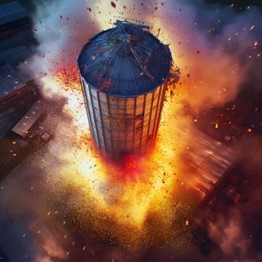
Figure 4 – Silo Explosion [5]
In the context of dust explosions, which are particularly hazardous in industries handling combustible dusts like wood, grain, chemicals, and metals, technical and engineering explosion protection measures are tailored to address the unique challenges posed by fine particulate matter. Let’s explore how these measures are applied specifically to mitigate dust explosions and the risks associated with them:
Explosion Venting
- Install explosion vents to release pressure during an explosion: Explosion venting involves installing vents or panels designed to open when an explosion occurs inside a vessel or building, releasing the pressure and dust flames safely into the atmosphere or a controlled area. This prevents the structural failure of containment systems, such as silos, dust collectors, or processing equipment, thus avoiding more catastrophic secondary explosions or structural collapses. For dust explosion scenarios, it’s crucial that the vented dust is directed to a safe area to prevent secondary fires or explosions caused by the expelled combustible dust.
Flameless Venting
- Use flameless venting systems to prevent flames from escaping: Flameless venting systems are particularly beneficial for indoor applications or where releasing the explosion into the surrounding environment could pose risks. These systems have a flame-arresting mesh or material that cools and extinguishes the flames from an explosion, allowing only the pressure wave and non-combustible gases to pass through. This technology is ideal for facilities where external venting is not practical or could pose a hazard, ensuring that operations involving combustible dusts can be carried out safely within buildings.
Explosion Suppression
- Deploy suppression systems to extinguish flames: For dust explosions, suppression systems are designed to detect the initial pressure rise of an explosion and then rapidly introduce a suppression agent (often a fine powder) into the vessel or duct. This suppressant quickly quenches the flame and reduces the pressure within milliseconds, preventing the explosion from fully developing. These systems are essential in process areas where containing an explosion is not feasible and where the rapid extinguishment can prevent a small incident from escalating into a larger, more dangerous event.
Explosion Containment
- Design structures to contain explosions: In facilities handling combustible dusts, certain processes or equipment might not be suitable for venting or suppression due to the nature of the materials or the process itself. In these cases, explosion containment involves designing and constructing equipment and structures (such as reactors, mills, or conveyors) to withstand the pressures generated by an explosion without rupturing. This ensures that even if an explosion occurs within the contained system, it does not lead to a breach that could propagate the explosion to other areas of the facility.
Deflagration Isolation
- Implement isolation systems to prevent flame propagation: Deflagration isolation is critical in preventing the spread of dust explosions through interconnected systems like ductwork or conveyors. This can be achieved using various isolation devices, such as fast-acting valves, chemical barriers, or flap valves, that close off a section of the system when an explosion is detected. By isolating the explosion to its origin point, these devices prevent the flame and pressure front from moving through the process system, significantly reducing the risk of secondary explosions and widespread damage.
Implementing these technical and engineering measures requires a thorough understanding of the materials being handled, the processes involved, and the specific risks present in a facility. By carefully designing and maintaining these protection systems, industries can significantly mitigate the impact of dust explosions.
Legal Framework – Irish and European Requirements
In Ireland and the European Union, several regulations and standards govern the prevention and mitigation of dust explosions.
Part 8 of the Safety, Health and Welfare at Work (General Applications) Regulations 2007
- Employers must ensure the safety, health, and welfare of employees, including measures related to explosive atmospheres.
Two ATEX directives apply throughout the European Union
- ATEX 137 99/92EC User Directive, this is transcribed directly into Irish law. This outline the minimum requirements for improving the safety and health protection of workers potentially at risk from explosive atmospheres.
- ATEX 2014/34/EU User directive, this is also transcribed into Irish law. This outlines the minimum requirements for equipment and protective systems intended for use in potentially explosive atmospheres.
By aligning with the legal requirements and implementing these strategies, organizations can significantly reduce the risk of dust explosions. Remember that prevention is the first line of defence, followed by effective control measures and proper explosion protection. Safeguarding personnel and assets requires a smart approach that addresses combustible dust hazards at every level.
Occupli Consultancy specialists provide practical solutions and advice to all our clients in all areas of ATEX related services. Our team work to legislative requirements and benchmark against industry best practice to produces assessments for our clients. Occupli Consultants have carried out ATEX risk assessments in a range of different industries which include the medical devices, pharmaceutical, agricultural, manufacturing and many more.
If you require ATEX services, reach out to our team of consultants here.